Fluid Dynamics Software and Pipe Simulation
FloCAD® is a fluid dynamics software add-on module for Thermal Desktop®, together they provide a complete thermohydraulic software tool for fully integrated fluid flow and heat transfer analysis. With FloCAD, the mechanics of building fluid flow models is very similar to that of building thermal models, with many of the commands applicable to both types of models. FloCAD models can be free-form (non-geometric), sketchpad style flow network modeling for abstraction and simplification, or they can be geometry-based by including objects such as pipe centerlines and cross-sections, complexly shaped vessels, or convection to finite difference of finite element representations of thermal structures.
Integrating Fluid Flow Networks with CAD-Based FEA or FDA
FloCAD provides the ability to model piping systems, heat transfer equipment and power cycles, tanks and vessels, and heat pipes. Single- or two-phase fluid systems can be modeled, as well as compressible and incompressible fluids, and fluid mixtures. Features include custom control systems, turbomachinery, chemically reacting flows, complex vessels with many ports and piping penetrations, and capillary and thermosiphon systems.
As a generalized pipe flow software tool, FloCAD captures the pressure drops in a piping network due to bends, valves, tees, changes in flow area, etc. As a full thermohydraulic software tool it also accounts for the acceleration terms associated with axial variations in velocity due to density, side flow, or the transient storage and release of mass in compressible tanks in addition to phase change associated with evaporation and condensation. Combining these pipe flow capabilities with FloCAD's geometric ports provides enhanced modeling of fluid flow entering and leaving complex tanks and vessels.
As with the rest of the Thermal Desktop suite, FloCAD includes full parameterization using spreadsheet-like variables and arbitrarily complex expressions as input, rather than hardwired numbers. This allows complex models to be rapidly manipulated using a few keystrokes, meaning that updating or maintaining a model is trivially easy, as is performing sensitivity studies and investigating what-if scenarios. This provides access to SINDA/FLUINT's Optimization and Reliability Engineering modules, which can be used to size components, maximize performance, find worst-case operating conditions (design cases), calibrate models to test data, and even treat uncertainties statistically.
Fluid Modeling Features
- Generates flow networks and calculates convective heat transfer factors for solution by CRTech's SINDA/FLUINT
- Uses CAD geometry directly, or accepts snap-on thermal surfaces
- Fluid flow networks can be based on geometry, or can be sketchpad-style, or both
- Integration with 2D/3D thermal structures, unlike non-geometric fluid network modeling tools
- Automatic connection and apportionment of convection links to thermal surfaces
- Postprocesses temperatures, pressures, flow rates, flow regimes, liquid fill levels, flow qualities, and void fractions for fast interpretation
- Faster model building and faster calculations than CFD enables system-level transient solutions, investigation of alternatives, sizing and sensitivities, and calibration to test or CFD data
- Arbitrary fluids including dry air, moist air (psychrometrics), water, water/glycol, cryogens, and dielectric fluids
- Accepts user-defined fluids as well
- Compartments and ports for fluid modeling of the flow in and out of complex tanks
Pipe Flow Devices and Components
- Full access to FLUINT flow network modeling capabilities, with abbreviated inputs for common components
- Full selection of turbomachines: pumps, fans, compressors, and turbines
- Flow passages and ducts, including complex pipes
- Filters and porous media
- Valves, venturis, orifices, tees, and loss elements, including PID and user-programmable control schemes
- Capillary evaporator pumps for Loop Heat Pipes (LHPs)
- Heat Pipes, constant and variable conductance (CCHP, VCHP)
- Fast-solving methods for analyzing complex vessels
- Locations of piping ports and penetrations on the sides or insides of vessels
- Heat exchanger modeling, from detailed to top-level system approximations and sizing
- Built-in K-factor calculator resistance utility for common fittings
- Specialized waterhammer features including complex Pipe walls, two-phase line priming events
Access to Thermal Desktop Modeling Tools
- User-defined symbols and expressions
- Rapidly propagate design changes
- Support for SINDA/FLUINT's Advanced Design Module: parametric modeling, optimization, model correlation, and reliability engineering
- Network element logic and indirect referencing automate the application of user customizations
FloCAD Connectivity
- FloCAD is an optional fluid flow simulation module of CRTech's CAD-based Thermal Desktop, which handles conduction and capacitance in surfaces and solids, features arbitrary (nongeometric) nodes, and supports FEM models including innovative automatic network simplification techniques, and mapping to structural analysis codes such as NASTRAN and ANSYS
- CRTech's TD Direct can be used to import virtually any CAD format, clean and defeature, then mark fluid convection zones (for example) and mesh
- Also available: RadCAD® for thermal radiation
- FloCAD is fully supported by the EZXY Plotter
How is FloCAD Different from other Computational Fluid Dynamics tools?
Nusselt and Reynolds vs. Navier and Stokes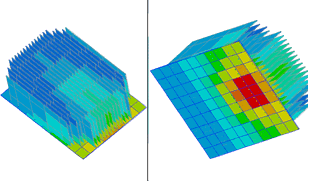
FloCAD is a 1D thermohydraulic (fluid network modeling, or “FNM”) expansion to the solid/surface thermal modeling tools within Thermal Desktop and RadCAD®. The result is a unique combination of 3D thermal/structural modeling plus 1D fluid flow simulation.
Many engineers are unfamiliar with this approach compared to the many commercial CFD (computational fluid dynamics) packages available. "How is FloCAD different from CFD?” is a common question. Some of the FloCAD capabilities, such as fuel motions within a multi-compartment tank, can even look like a CFD result.
Fast-solving correlation-based methods such as FloCAD have important advantages that will persist even as computers and CFD methods continue to improve in the future. This isn't an "either/or proposition:" FloCAD doesn't compete directly with CFD since both types of fluid modeling have their own strengths for certain applications. In fact, an integrated FloCAD/CFD approach can be very useful for many classes of fluid modeling problems.
Advantages of the FloCAD Approach
FloCAD uses a fast-to-build, fast-to-solve empirical approach: the exact details of the geometry are often avoided by applying heat transfer and pressure drop correlations such that a one dimensional flow field is adequate. Simply put, the FloCAD approach eliminates the need for extra meshing. This choice has many repercussions:
- Cost: The purchase price of the FloCAD suite of tools is much less than that of comparable CFD software. In addition, the time required to learn and retain FloCAD is reduced, as is the time required to build and change models.
- Speed: The solution speed of FloCAD is orders of magnitude faster than that of CFD approaches: meaningful results can be obtained within minutes on a single PC.
- This means being able to ask “bigger questions” at either higher levels of assembly or what-if and sensitivity studies using parametric modeling and Advanced Design Modules (for optimizing, calibrating to test, statistical design including tolerancing, etc.).
- Phenomena: Transient system-level analyses are not a problem for the FloCAD approach, and it makes quick work of systems that are poorly suited for 3D CFD methods, including ducted air or coolant flows, heat pipes, and two-phase flow.
- Less accuracy? There is a common presumption that CFD methods assume less than correlation-based approaches, and are therefore more accurate. Correlation-based methods like FloCAD do make assumptions such as fully-developed flow profiles, and such default assumptions are not always applicable. Those discrepancies must be overcome by additional guidance from the user. However, it is less commonly recognized that CFD methods struggle with heat transfer solutions because heat transfer is estimated based upon the flow field estimation: errors in heat transfer coefficients on the order of 20% are not uncommon when using CFD. Resolutions of this problem include use of even more fine meshes near the walls (causing even less flexibility and slower solution speeds) and, ironically, application of empiricisms.
Advantages of the CFD approach
The main advantage of CFD over FloCAD thermohydraulic methods is that certain classes of 2D/3D flow problems that are simply not amenable to 1D methods, or at least require too much user involvement (for example, correcting for entrance length effects or specifying losses influencing flow splits) to exploit 1D flow solution methods and available heat transfer correlations.
Nonetheless, many engineers continue to use both methods for such problems. Essentially, they use a CFD solution to develop a correlation for use in codes such as FLUINT: using CFD runs to define a flow split, a pressure or velocity boundary condition, an effective loss or heat transfer coefficient, etc. Using these as inputs to SINDA/FLUINT enables modeling of transients, parametric solutions, optimization, calibrations to test data, two-phase flow solutions, and so forth.
CFD programs can produce postprocessed 3D flowfields and streamlines, which certainly have tremendous appeal in presentations and technical papers, but they can also help build intuition.